Gate Valve
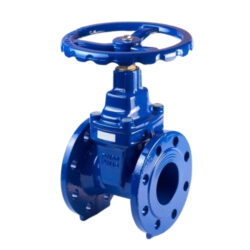
A gate valve, also known as a sluice valve, is a valve that opens by lifting a barrier (gate) out of the path of the fluid. Gate valves require very little space along the pipe axis and hardly restrict the flow of fluid when the gate is fully opened. The gate faces can be parallel but are most commonly wedge-shaped (in order to be able to apply pressure on the sealing surface). Gate valves are used to shut off the flow of liquids rather than for flow regulation. When fully open, the typical gate valve has no obstruction in the flow path, resulting in very low flow resistance. The size of the open flow path generally varies in a nonlinear manner as the gate is moved. This means that the flow rate does not change evenly with stem travel. Depending on the construction, a partially open gate can vibrate from the fluid flow.
Blow Poppet Valve
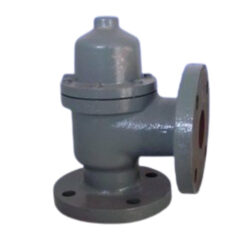
Blow Poppet Valve is specially design for air purging or blow air in pneumatic conveying systems. A valve is actuated with instrument air pressure which is easily controlled by a solenoid valve. Blow poppet valve is a pneumatically piston operated type on-off type valve. Having low minimum moving part so that longer valve life. Which is used in the pneumatic conveying system for supplying purging air into the ash transmitter vessels, Hoppers, and conveying Line. Blow Poppet Valve is known for its low torque, less friction, and long service life. Technologically advanced machinery at our unit assists in the smooth functioning and operating of our Blow Poppet Valve so that it meets the demands of our clients efficiently and effectively.
Dome Valve
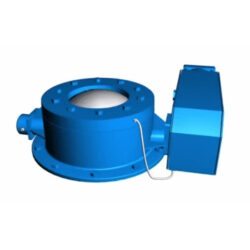
Dome Valve: When open, it allows an unobstructed flow path to material ensuring prolonged life, making it most reliable and least maintenance prone. An inflatable pneumatic sealing ensures an airtight seal in a closed position which provides a dust-free environment and saves energy. Dome cuts through the moving or static column of material ensuring proper closing. A mere quarter turn is sufficient to move the dome valve from “closed” to “open” position. Unique features make the Dome Valve inherently more efficient, highly reliable, and long-lasting as compared to other types of valves like a butterfly, cone, plate, flap, etc. Dome valve’s capability to open & close with tight pressure seal works efficiently in harsh environments for abrasive materials. The valve finds its application in Power Generation, Cement, Iron, Mineral, Ferrous / Non-ferrous, Chemical, etc industries for bulk material handling.
Globe Valve
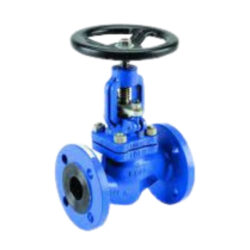
A globe valve, different from ball valve, is a type of valve used for regulating flow in a pipeline, consisting of a movable plug or disc element and a stationary ring seat in a generally spherical body. Globe valves are named for their spherical body shape with the two halves of the body being separated by an internal baffle. This has an opening that forms a seat onto which a movable plug can be screwed in to close (or shut) the valve. The plug is also called a disc. In globe valves, the plug is connected to a stem which is operated by screw action using a handwheel in manual valves. Typically, automated globe valves use smooth stems rather than threaded ones and are opened and closed by an actuator assembly.
Check Valve
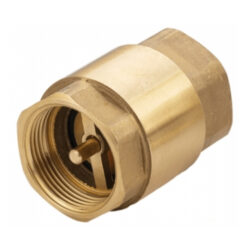
Check valves are two-port valves, meaning they have two openings in the body, one for fluid to enter and the other for fluid to leave. There are various types of check valves used in a wide variety of applications. Check valves are often part of common household items. Although they are available in a wide range of sizes and costs, check valves generally are very small, simple, and inexpensive. Check valves work automatically and most are not controlled by a person or any external control; accordingly, most do not have any valve handle or stem. The bodies (external shells) of most check valves are made of plastic or metal. An important concept in check valves is the cracking pressure which is the minimum differential upstream pressure between inlet and outlet at which the valve will operate. Typically the check valve is designed for and can therefore be specified for a specific cracking pressure.
Ball Valve
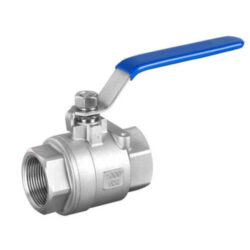
A ball valve is a flow control device that uses a hollow, perforated, and pivoting ball to control liquid flowing through it. It is open when the ball’s hole is in line with the flow inlet and closed when it is pivoted 90-degrees by the valve handle, blocking the flow. The handle lies flat in alignment with the flow when open, and is perpendicular to it when closed, making for easy visual confirmation of the valve’s status. The shut position 1/4 turn could be in either or counter-clockwise direction. Ball valves are durable, performing well after many cycles, and reliable, closing securely even after long periods of disuse. These qualities make them an excellent choice for shutoff and control applications, where they are often preferred to gates and globe valves, but they lack the fine control of those alternatives, in throttling applications.
Bellow Seal Valve
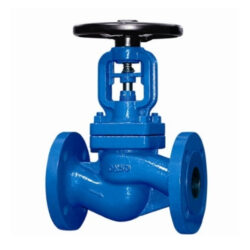
The bellows valve’s stem is double sealed by the bellows and the packing, often used where it needs the strict sealing performance of valve stem. Metal bellows can produce the corresponding displacement under the action of pressure, transverse force or bending moment, and has the advantages of pressure resistance, corrosion resistance, temperature stability and long service life. Bellows can improve the sealing performance of the valve stem and protect it from the corrosion of medium, suitable for heat transfer media of polyester industry, ultra-vacuum and nuclear industry.
Swing Check Valve
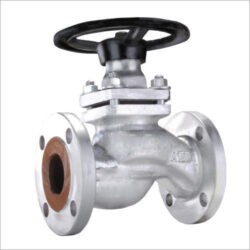
A piston valve is a device that is used to control the motion of a fluid along a tube or pipe by means of the linear motion of a piston within a chamber or cylinder. Piston valves are used for fully open or fully closed for on/off regulation on steam, gas, and other fluid services. These valves are mostly used on fluids which cause excessive seat wear. Piston valves are mostly actuated manually, but some-times other actuation modes such as hydraulic and electric are used. Piston valves are usually used where the valve body is permanently installed and to reduce maintenance. Piston valves are not designed for throttling applications and they must be used in fully opened or closed positions. When the valve is fully opened, only the bottom face of the piston is exposed to fluid and the rest of the body is protected by the upper sealing rings. So the sealing surfaces are protected from erosion by the fluid flow.
Piston Valve
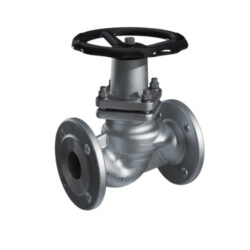
A piston valve is a device that is used to control the motion of a fluid along a tube or pipe by means of the linear motion of a piston within a chamber or cylinder. Piston valves are used for fully open or fully closed for on/off regulation on steam, gas, and other fluid services. These valves are mostly used on fluids which cause excessive seat wear. Piston valves are mostly actuated manually, but some-times other actuation modes such as hydraulic and electric are used. Piston valves are usually used where the valve body is permanently installed and to reduce maintenance. Piston valves are not designed for throttling applications and they must be used in fully opened or closed positions. When the valve is fully opened, only the bottom face of the piston is exposed to fluid and the rest of the body is protected by the upper sealing rings. So the sealing surfaces are protected from erosion by the fluid flow.
Swing Check Valve
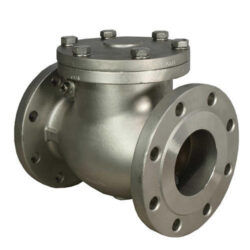
A swing check valve is mounted with a disc that swings on a hinge or shaft. The disc swings off the seat to allow forward flow and when the flow is stopped, the disc swings back onto the seat to block reverse flow. The weight of the disc and the return flow has an impact on the shut-off characteristics of the valve. Swing check valves with lever and weight or lever and spring often a lever and weight or a lever and spring are mounted to achieve optimum performance. Swing check valves with lever and weight are appropriate for installations with an increased risk of water hammer at standard velocities. Swing check valves with lever and external spring are suitable for high pressure, insufficient backpressure, and high flow velocities. An important thing to be aware of when installing a swing check valve is, that it is not completely maintenance-free since the disc needs to be cleaned once in a while. Furthermore, a lever is often mounted to enable visual check.
Knife Gate Valve
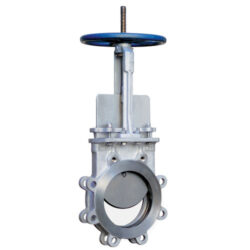
Knife gate valves are designed mainly for on-off and isolation services in systems with high content of suspended solids. Knife gate valves are especially beneficial for handling slurry, viscous, corrosive and abrasive media. The valves have a minimised pressure drop in fully open position, they are easy to actuate, they have a relatively low weight and are cost effective. Knife gate valves are designed to work in some of the harshest environments, typically having a sharpened blade to cut through heavy liquids. Knife gate valves should only be used for applications requiring a completely open or completely closed position and should not be used to regulate flow unless they are designed for it. Whenever fluid is forced against a partially closed gate, there will be a vibration, gradually eroding the disc and seat. In addition, the knife gate valves are designed to slowly open and close to safeguard against the impacts of water hammer.
Y Strainer
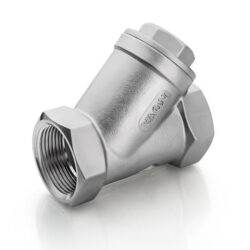
Y-Strainers are devices for mechanically removing unwanted solids from liquid, gas or steam lines by means of a perforated or wire mesh straining element. They are used in pipelines to protect pumps, meters, control valves, steam traps, regulators and other process equipment. Y-Strainers are very cost effective straining solutions in many applications. Where the amount of material to be removed from the flow is relatively small, resulting in long intervals between screen cleanings, the strainer screen is manually cleaned by shutting down the line and removing the strainer cap. For applications with heavier dirt loading, Y-Strainers can be fitted with a “blow-off” connection that permits the screen to be cleaned without removing it from the strainer body. Y-Strainers are used in a wide variety of liquid straining applications to protect downstream process system components in many industries, including chemical processing, petroleum, power generation and marine.
Visi Flow
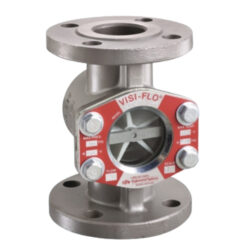
All areas of moulded component creation can benefit from the optimisation of mould tool design and moulding process parameters. Part designers, mould makers and moulders will all benefit from using Mechsignia innovative technology for injection simulation to achieve cost effective and reliable mould designs and the optimum moulding conditions. VISI Flow is a unique prediction tool, ideal for pre and post production analysis and concurrent engineering of injection moulded plastic components. Visi-Flo Indicators are designed for applications with maximum operating pressures of 400 psig (27.6 bar) and/or temperatures of 350ºF (177ºC). The Visi-Flo Series requires no special maintenance or torqueing sequence and end-to-end dimensions.
Rotary Airlock Valve
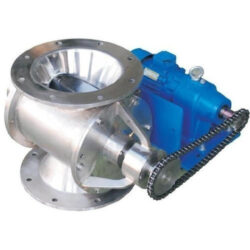
Rotary airlock valves are also called rotary feeders, rotary valves, or just rotary airlocks. Used in both pressure style and vacuum style pneumatic conveying systems, these valves serve as a “lock” to prevent air loss while simultaneously performing vital material handling functions. Though simple, the rotary airlock valve is a critical component to the efficiency of a conveying system. It’s important to remember that not all rotary valves are necessarily rotary airlock valves – but virtually all rotary airlocks are rotary valves. The vanes, or metal blades, of a rotary airlock valve turn (rotate) during operation. As they do, pockets form between them. The material being handled enters the pockets through the inlet port before rotating around inside the valve and then exiting through the outlet port. In an airlock valve, air is sealed (locked) between the inlet and outlet ports. This allows the materials to travel downward through the valve from the inlet to the outlet port while restricting the airflow.